Deep Tray is a non-combustible
cavity tray solution designed with ease
and safety of installation in mind
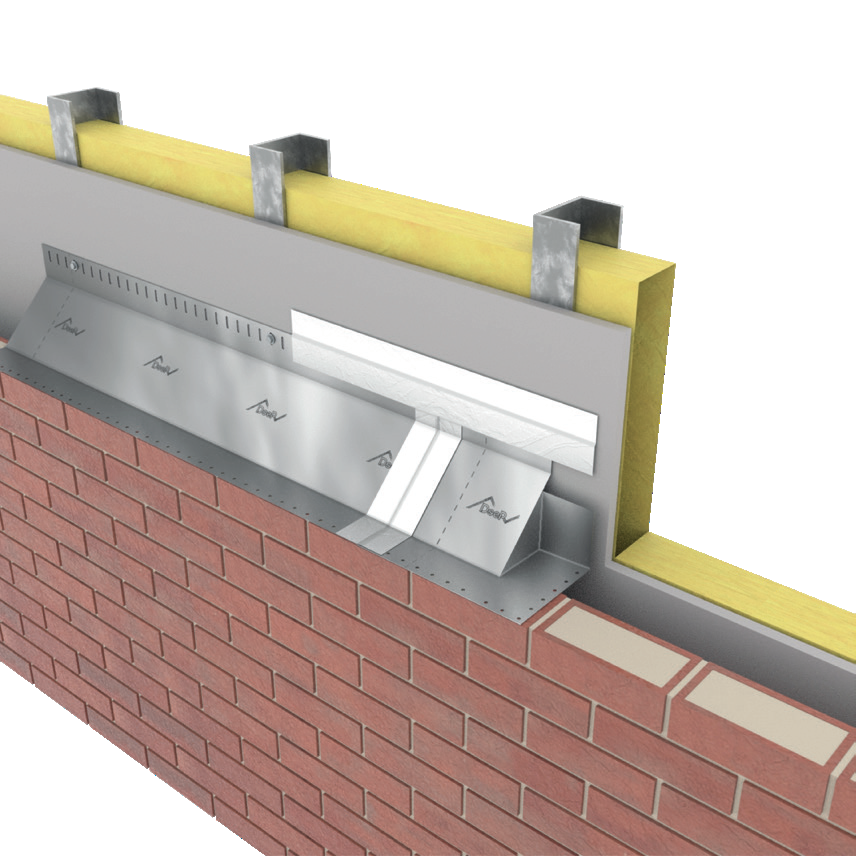
An Introduction to Deep Tray
With extensive experience in different elements of façade construction, Deep Group London is ideally placed to design and develop innovative and versatile systems to meet changing market needs.
The Deep Tray non-combustible cavity tray solution represents the latest milestone in a 10-year history of success, which has seen the company established as one of the fastest growing organisations of its kind.
Deep Tray is created bespoke to suit the individual client’s needs as we understand each requirement is unique.
Our solution
Developed to meet all types of design situations for cavity interruptions around doors and windows above 18 metres, the Deep Tray system is a full suite of noncombustible cavity tray components. This includes over door or window lintel, window or door brick reveal stop ends, door or windowsill and accessories. Each component is specifically designed for each project to provide a structurally proven, non-combustible alternative to traditional DPCs.
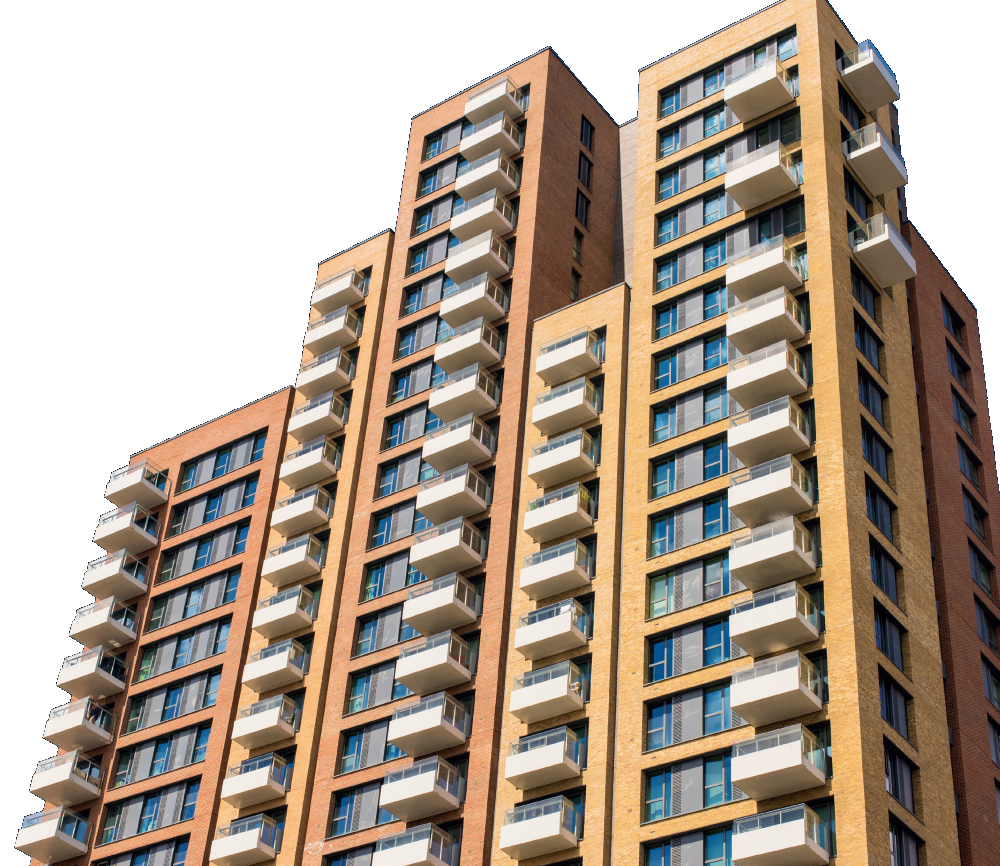
Product Features
Non-Combustible
Can be made bespoke to suit clients requirements and specifications
Lightweight and versatile
Fast delivery and installation
Designed for safe handling on site
Manufactured in 304 or 316 Stainless Steel
Tested by Lucideon Labs
Conforms to fire certification criteria
UK manufactured
Accreditations

Performance
Deep Tray has been designed to perform. The system provides long-term protection against corrosion and heat.
Corrosion Resistance & Heat Resistance
Due to the material used in the manufacture of Deep Tray – stainless steel – the system offers excellent corrosion resistance, making it ideal for a wide range of environments.
Stainless steel also has a great resistance when it comes to oxidisation in intermittent service at 870º C and in continuous service to 925º C. If, however, there is continuous use at 425 to 860º C this is not recommended if corrosion resistance in water is required due to its resistance to carbide precipitation.
Weldability
Deep Tray is suitable for fusion welding. The performance of stainless steel means it can be used with or without fillers. Recommended filler rods and electrodes for 316 and 316L are the same as the base metal.
Meeting Legislative
Requirements
Approved Document B of the Building Regulations provides guidance on meeting fire safety requirements.
Deep Tray meets this requirement by providing a noncombustible solution to help safely deliver building façades.
The principal building regulation requirement in relation to the external walls of buildings is requirement B4 (1) which states ‘the external walls of the building shall adequately resist the spread of fire over the walls and from one building to another, having regard to the height, use and position of the building’.
A recent review of ADB has seen Government ban combustible materials on high-rise buildings by amending Regulation 7 of the Building Regulations and ADB so that materials which become part of an external wall of a high-rise building now have to be of European Classification A2-s1, d0 (i.e. of limited combustibility) or Class (non-combustible).
Building Regulations Document B
(Fire Safety) 2019 Edition
Recent updates to Building Regulations stress the prohibition of combustible materials usage within the external cavities of buildings over 18m in height (soon to be 11m). This applies to buildings containing one or more dwellings; an institution or a room for residential purposes (excluding any room in a hostel, hotel or boarding house, but including student accommodation, care homes, sheltered housing, hospitals and dormitories in boarding schools).
As Deep Tray is manufactured entirely from 304 or 316 stainless steel which is recognised by the European Commission as an A1 fire rated classified material – the highest level of fire safety performance – no additional testing is required to prove its non-combustible properties.
Tray & Brick Reveal Stop End
Our Tray & Brick Reveal Stop End is an effective method of preventing dampness permeating the internal skin of the wall. With a wholly intuitive install, the cavity tray offers a long lasting solution to threat of water damage to the property.
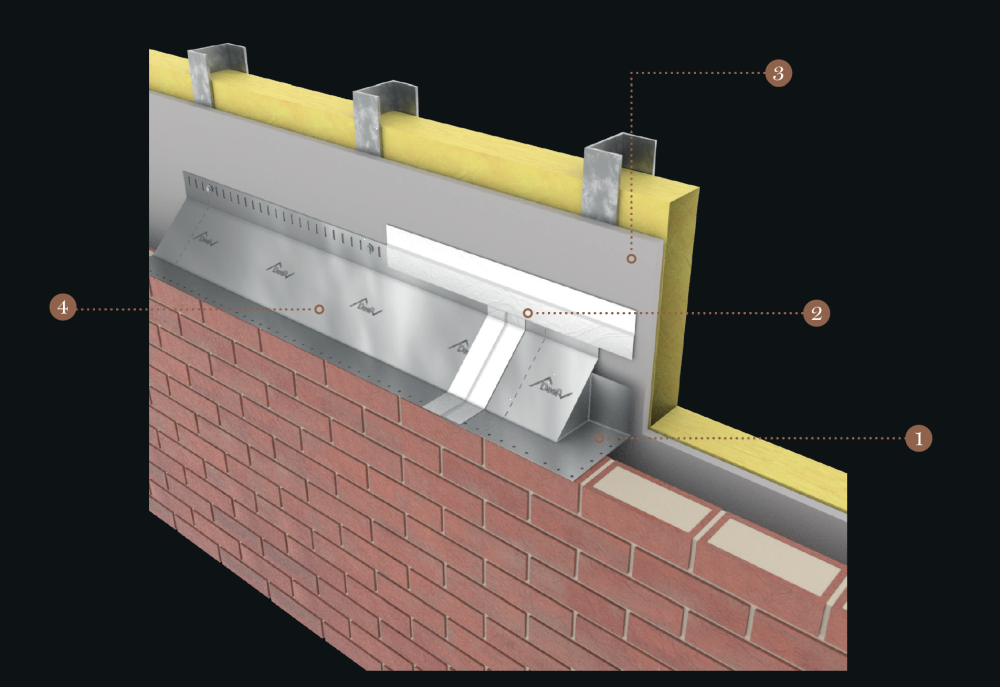
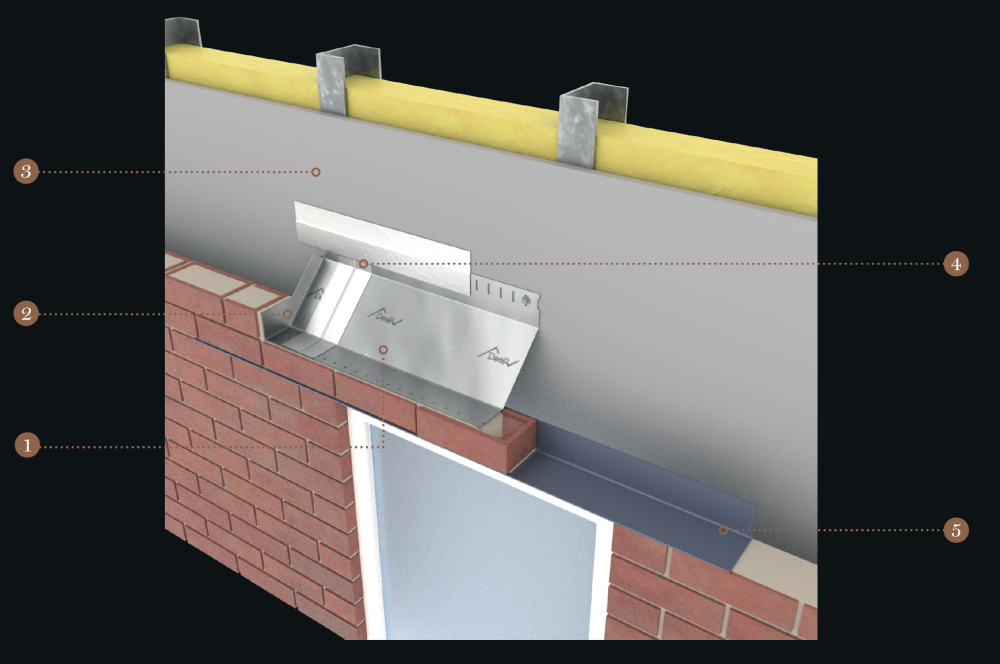
Over Door/Window Lintel
External Corner & Stop End
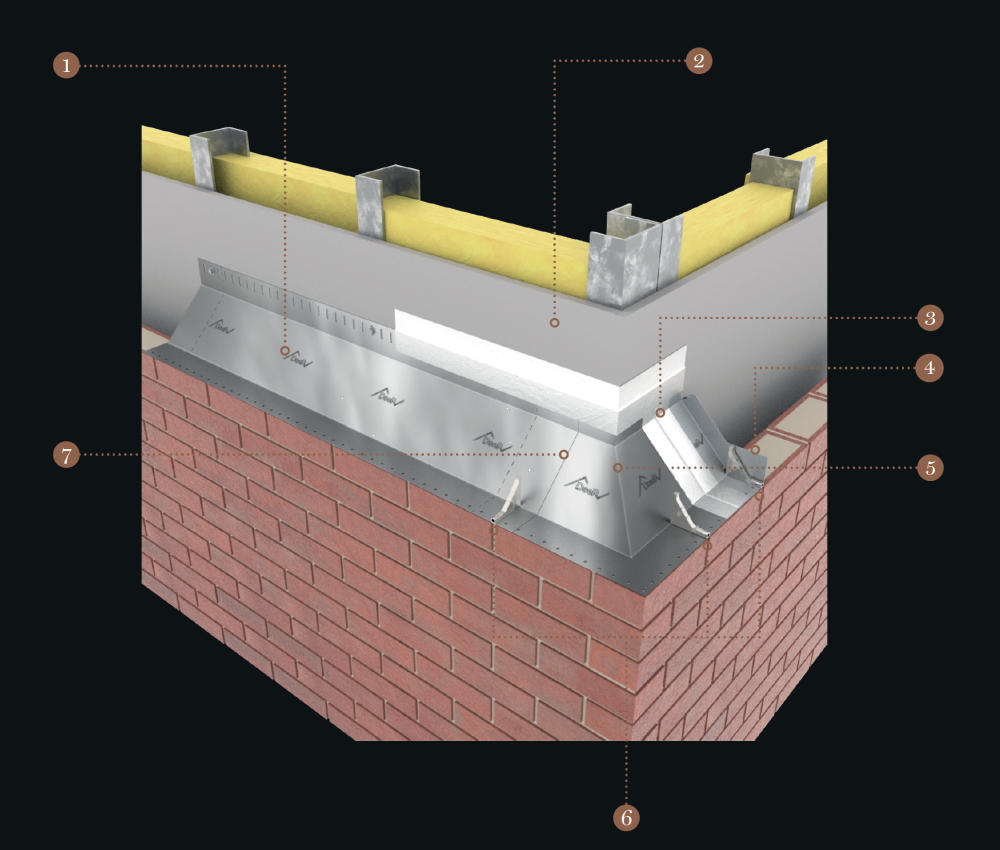
Components

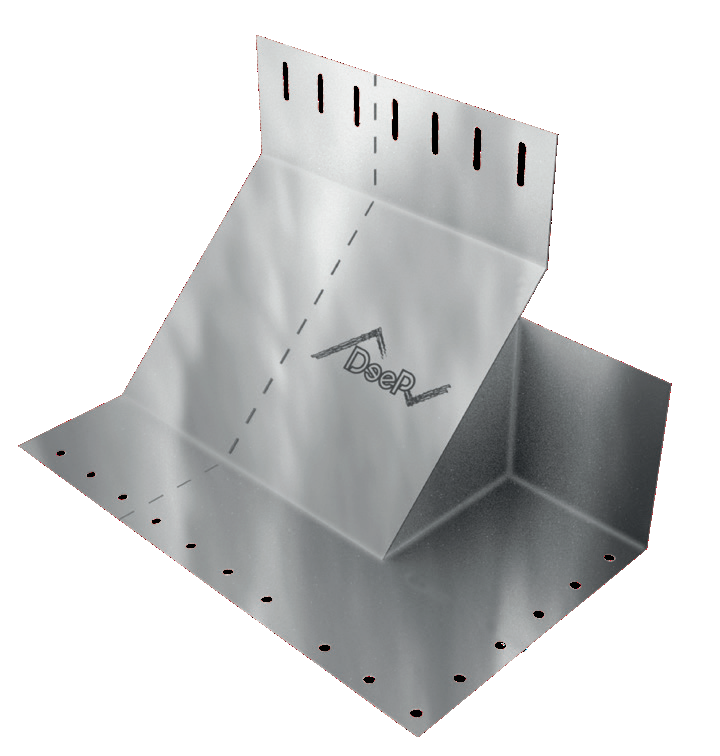
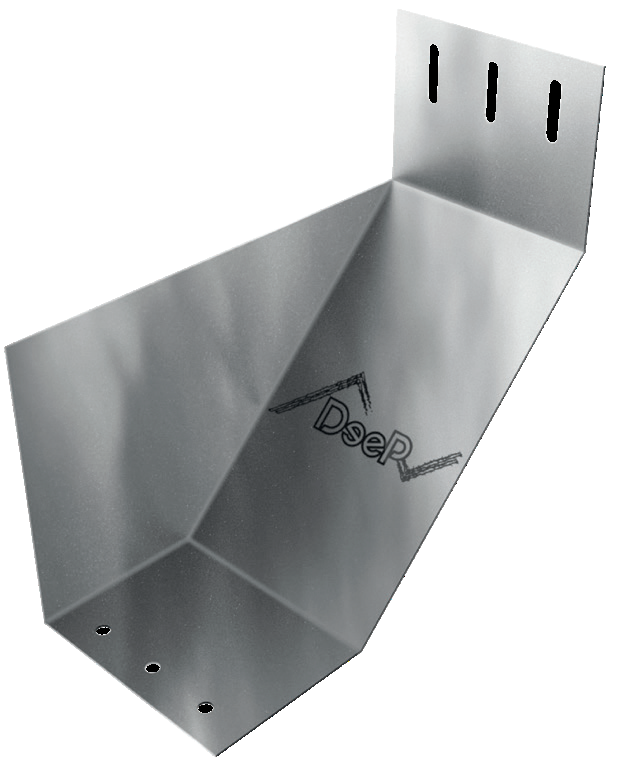
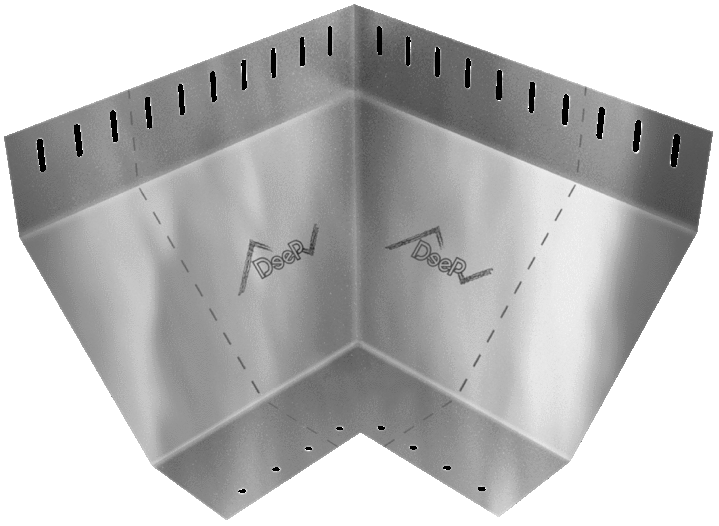
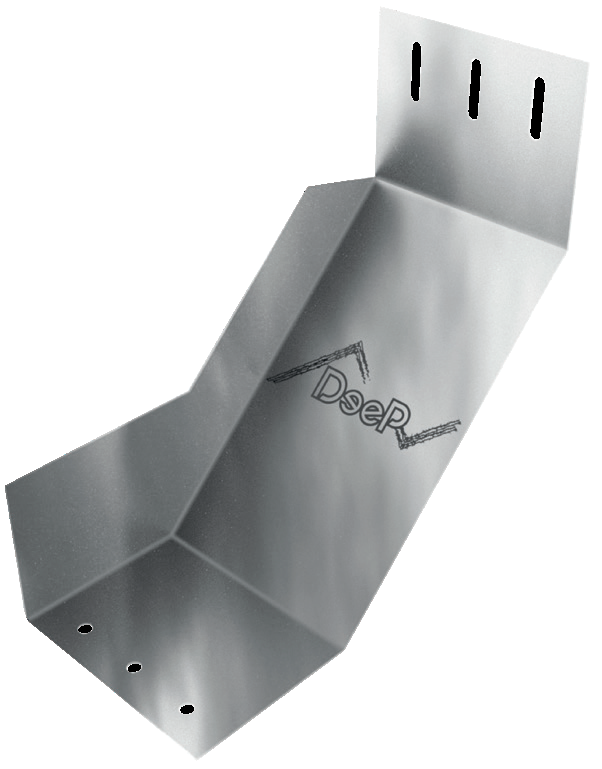
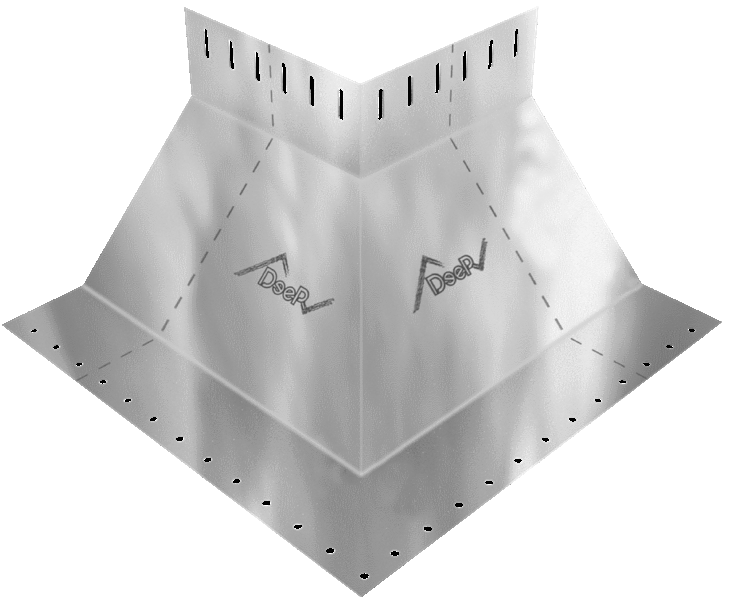
Installation
Deep Tray components are designed to be lightweight and easy to install, and user friendly
to handle on-site. See the outlined method below for installation:
1
Appropriate PPE including safety gloves should always be worn when handling stainless steel cavity trays.
2
3
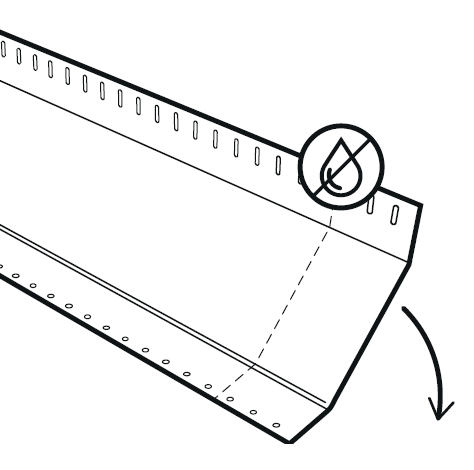
4
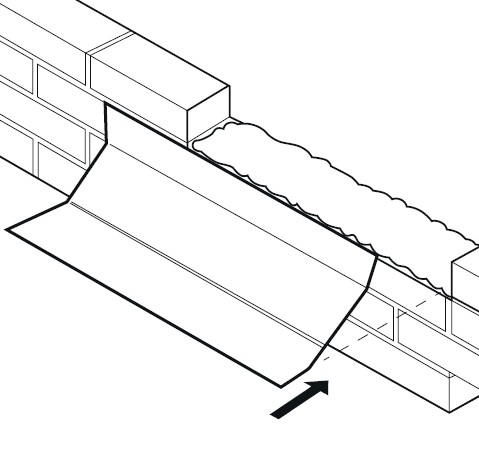
5

6
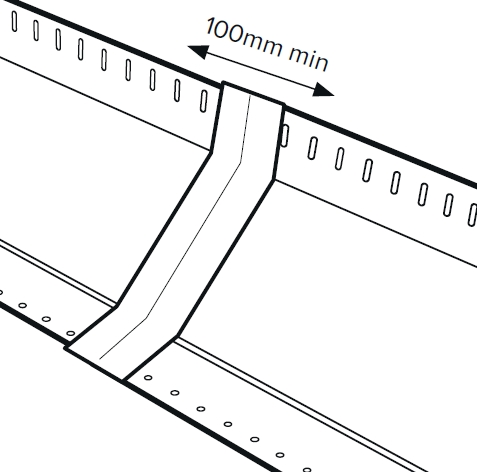
7
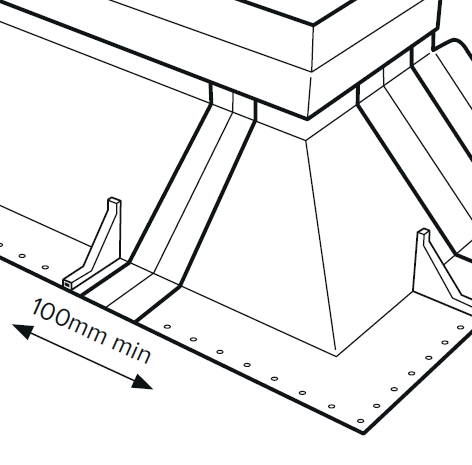
8
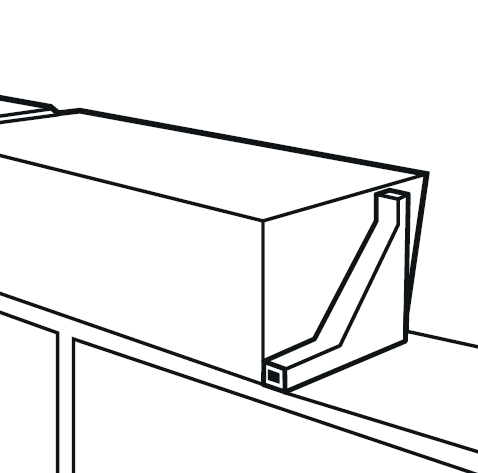